Vibration Monitoring Solutions.
Detect anomalies in real-time, optimise maintenance + prevent breakdowns, simply.
Easily create a custom Vibration Monitoring solution that delivers real-time, traceable performance improvements.
Monitor + manage real-time air quality and pollution with a custom, real-time solution.
Take asset and machinery monitoring to the next level using our advanced vibration monitoring solution tailored for businesses.
Use our Rayven Platform's Vibration Monitoring solution template as your starting point and integrate infield devices, third-party systems, and assets to deliver real-time and predictive insights on performance and how it can be improved.
Our all-in-one, easy-to-use technology comes complete with universal integration, machine learning, automation, and AI capabilities; enabling you to detect potential problems, streamline maintenance schedules, and optimise overall equipment performance.






Remote, real-time vibration monitoring from anywhere.
Predict maintenance needs + prevent failures.
Build interactive dashboards + drill into trends.
Add custom AI + universal automation.
Fits all existing
hardware + technologies.
Add additional vectors, including heat, noise + speed.
Monitor assets for excessive vibrations. Integrate real-time data sources from sensors, systems, and machinery software to get the complete, real-time view.
Set-up normal performance thresholds, alert employees of anomalies, and create custom automations and logic that shuts machinery down before major failures.
Build custom dashboards to explore individual asset's and fleets' performance. Explore potential causes, how other variables interact, and analyse historical data sets, fast.
Our solution enables you to use predictive analytics with your real-time data to predict future performance and maintenance needs.
Our vibration monitoring solution will integrate with any machinery, system, hardware, sensor, technology, or data repository - guaranteed
Incorporate different in-field sensors to develop a complete, real-time view of machine performance + enhance predictive modelling.
Rayven has free + low-cost options, making it affordable for every business.
How your Vibration Monitoring solution is put together.
New and existing data, (both real-time and historical), alongside custom logic, thresholds, and predictive analytics is used to create your custom Vibration Monitoring solution.
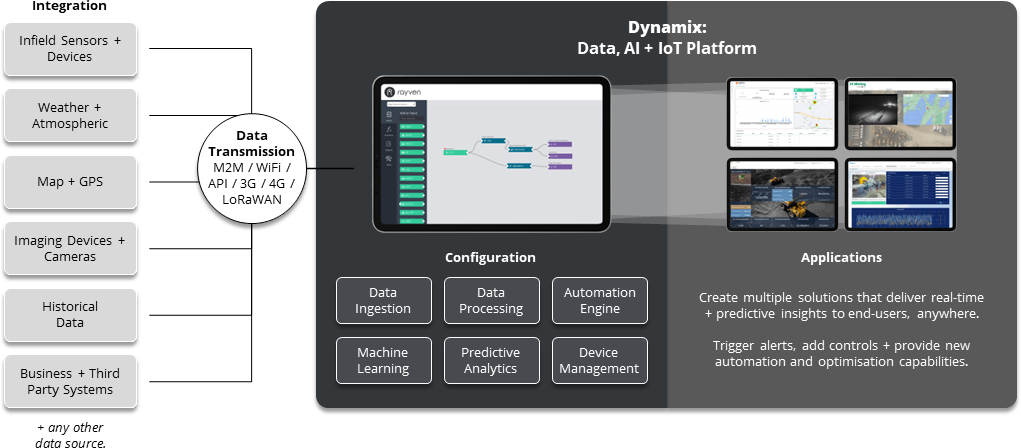
Our solution can handle data from anywhere in any format, and at all levels:
Level 1 Data: Manual entry of data via custom forms built within our solutions.
Level 2 Data: Bespoke spreadsheet ingestion via FTP or manual uploads.
Level 3 Data: Integration of real-time data from OT / IT systems and corporate systems.
Level 4 Data: Real-time integration with in-field technologies, asset systems + in-field sensors.



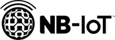

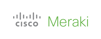







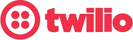

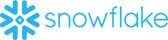
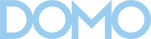

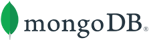
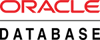
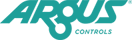


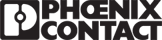
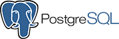
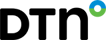
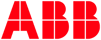


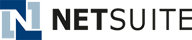

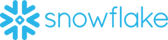




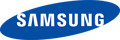
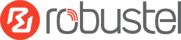


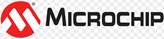





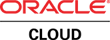

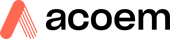

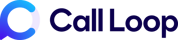
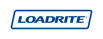



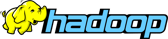
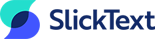
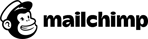

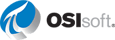
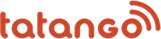


Your Vibration Monitoring solution will integrate with anything, including:


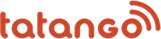
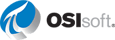

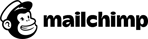
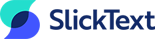

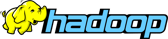




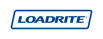

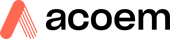

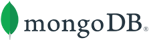

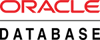




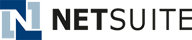
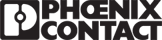

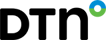
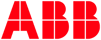
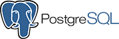

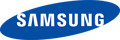
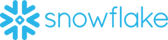

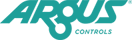


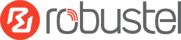


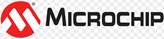





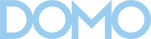
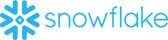

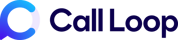
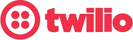





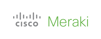

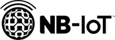



Vibration monitoring solution FAQs.
Question: What is vibration monitoring, and why is it important?
Vibration monitoring refers to the process of measuring and analysing vibrations produced by machinery and equipment, particularly in industrial settings. It is crucial for detecting early signs of mechanical issues, optimising maintenance schedules, minimising downtime, reducing costs, and improving overall equipment performance.
Question: What industries can benefit from vibration monitoring solutions?
Industries such as manufacturing, power generation, oil and gas, mining, and transportation can benefit from vibration monitoring solutions. Any sector where machinery and equipment health is vital to operations can utilise vibration monitoring to maintain optimal performance and reduce potential failures.
Question: How does an IoT-based vibration monitoring system work?
IoT-based vibration monitoring systems use connected devices, such as sensors, to continuously measure and track vibrations in real-time. The data collected by these devices is sent to a central platform for analysis and reporting, enabling businesses to make informed decisions and implement effective maintenance strategies.
Question: What are the key features to look for in a vibration monitoring solution?
Essential features to consider in a vibration monitoring solution include real-time data collection, accurate and reliable sensors, user-friendly data visualisation and reporting tools, alerts and notifications for potential issues, and the ability to integrate with existing systems and processes.
Question: How can real-time vibration monitoring help improve equipment maintenance?
Real-time vibration monitoring enables businesses to detect potential mechanical issues before they escalate, allowing for proactive maintenance and preventing costly equipment failures. By optimising maintenance schedules based on actual equipment health, businesses can minimise unexpected downtime, maximise uptime, and reduce maintenance costs.
Unlocking the power of real-time vibration monitoring in industrial applications.
Real-time vibration monitoring, powered by IoT technology, offers a proactive approach to managing equipment health and performance; and can be used for multiple applications that compound the benefit of any site-wide vibration monitoring solution.
- Early detection of equipment issues: Vibration monitoring enables businesses to identify early signs of mechanical issues in machinery, such as bearing wear, misalignment, or imbalance. By detecting these issues before they escalate, companies can prevent costly failures and extend equipment lifespans, as well as minimising downtime and maximising uptime.
- Optimised maintenance schedules: Traditional preventive maintenance schedules are set at fixed intervals, which in turn can lead to unnecessary or untimely servicing. With IoT-based vibration monitoring, businesses can transition to a condition-based maintenance approach, where maintenance is performed based on the actual health of equipment. This data-driven strategy reduces maintenance costs, optimises resource allocation, and prevents unexpected breakdowns.
- Improved Overall Equipment Effectiveness (OEE): Monitoring vibrations in real-time can contribute to improved overall equipment effectiveness. By identifying potential issues, optimising maintenance schedules, and reducing downtime, businesses can maintain high levels of equipment performance and availability.
- Enhanced worker safety: Unexpected equipment failures can pose significant safety risks to workers in industrial environments. Real-time vibration monitoring helps mitigate these risks by detecting mechanical issues before they escalate and even shutting down machines before a catastrophic and hazardous failure.
- Seamless integration with existing systems: IoT-based vibration monitoring solutions can be easily integrated into existing systems and processes. With user-friendly data visualisation and reporting tools, businesses can quickly access and analyse vibration data alongside other critical operational metrics. This comprehensive view of equipment health and performance enables informed decision-making and drives continuous improvement.
How can we help you get started?
Got this far? Explore all of Rayven's features.
