Yield Optimisation Solutions.
Improve production + profits using real-time optimisations, simply.
A Yield Optimisation solution built on Rayven can provide you with accurate, real-time production and sustainability metrics + all-new capabilities to improve profitability.
Increase yields, prevent breakdowns + find efficiencies, fast.
Your operation is unique and made up of its own technologies, processes and people; so solutions designed to improve performance must be able to fit your business as it is without the need to stop or disrupt what works.
Use our Rayven Platform's Yield Optimisation solution template as your starting point and integrate infield devices, third-party systems, and assets to deliver real-time and predictive insights on performance and how it can be improved.
Our all-in-one, easy-to-use technology comes complete with universal integration, machine learning, automation, and AI capabilities; enabling you to improve your operations, maintenance + output, simply.

Increased Yields + Throughput.
Understand the causes of yield losses and rework so that you can drive the continuous improvement of your production lines.

Increase Efficiency + Reduce Costs.
Monitor energy, water and resource use across operations and lines; spot inefficiencies; then model and test optimisations to save costs.

Predict Machinery Failure + Reduce Downtime.
Identify machine vibrations, noise and heat to identify future failures and guide fixes. Understand causes of downtime and drive uptime.

Improve Quality + ROA.
Quality defects can be isolated by location on a line, providing you with information vital to quality improvement actions.

Improve Sustainability.
Get accurate, real-time sustainaPlace data in the hands of your staff and you’ll improve engagement in continuous improvement and drive better outcomesbility metrics and use predictive analytics to plot a pathway to achieving objectives.

Improve Employee Performance.
Incorporate different in-field sensors to develop a complete, real-time view of environmental performance + enhance predictive modelling.
Driving measurable outcomes from our Yield Optimisation solutions:
Lower cost of maintenance
-4%
Increase utilisation
+5%
Reduce breakdowns
-7%
Increased throughput
10t
Productivity across shifts
+4%

Featured solution:
Factory One.
Factory One is a ready-to-deploy solution that helps manufacturers be more transparent, sustainable + productive.
Utilising our world-leading Rayven Platform; we have created a next generation, easy-to-use Industry 4.0 Smart Factory solution that improves yields, sustainability, and efficiency at manufacturing businesses both large and small.
Requiring no new hardware, Factory One creates a real-time single source of truth and features ready-to-deploy modules that improve different aspects of your manufacturing operations, giving you everything you need to solve complex real-time visibility and optimisation challenges, fast.
Factory One enables you to:
Increase throughput, quality + yields.
Lower cost of maintenance.
Improve sustainability.
Decrease energy + resource usage.
Reduce unplanned downtime.
Enhance productivity across shifts.
Discover some of Rayven's Yield Optimisation solutions' real-world use cases.
Food Production
Efficiency
Our client was concerned about yield losses, product giveaway, and an inability to reach daily production targets. We solved their business problems and improved OEE with a solution that provides vital information in real-time on key machines in the production process. Read More.
Improving Manufacturing OEE in Food + Beverage
Measuring manufacturing OEE is best practice, but doing it accurately, consistently, and in real-time, can be a significant challenge for many manufacturers - that's where Rayven's Manufacturing solution comes in: OEE Dynamix. Read More.
Real-time OEE + Machine Utilisation Monitoring
See how Rayven helped this milk bottling facility meet the highest food handling standards by enabling our client to understand their production and OEE in real-time. Read More.
Cold Storage Monitoring, Compliance + Energy Efficiency
Discover how our solution enabled our customer to better monitor their cold storage environment, ensuring that their products are stored at the correct temperatures and that they comply with food storage regulations, both during storage and in transport. Read More.
Plastic Recycling Plant Energy Efficiency
Improving the efficiency of a plastics recycling plant through the use of energy efficiency technology did much more than provide clarity over costs - it enabled savings to be found that made a significant impact on profitability. Read More.
Greenhouse Management, Monitoring + Yield Optimisation
The rapid growth in demand for non-traditional crops, as well as ongoing demand for fresh fruit and vegetables year-round, has created opportunities for greenhouse farming, but has also placed pressure on delivery, costs and product quality. Read More.



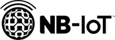

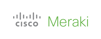







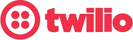

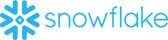
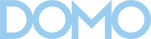

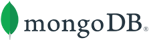
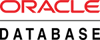
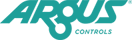


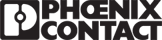
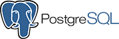
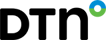
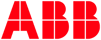


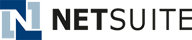

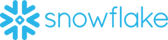




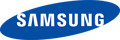
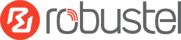


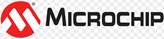





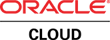

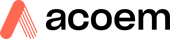

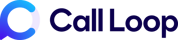
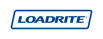



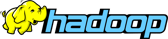
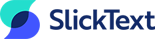
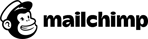

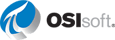
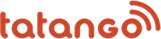


Your Yield Optimisation solution will integrate with anything, including:


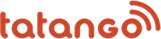
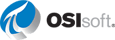

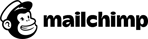
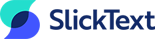

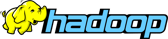




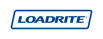

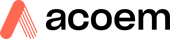

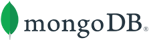

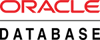




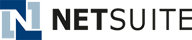
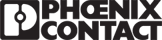

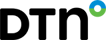
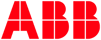
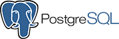

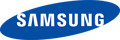
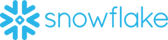

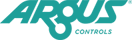


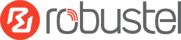


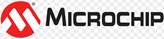





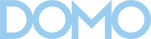
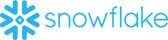

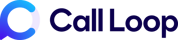
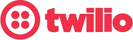





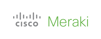

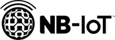



Free Manufacturing Applications Insights:
Welcome to Industry 4.0 or the Fourth Industrial Revolution! A product of the digital age, Industry 4.0 advancements have paved the way for industrial technologies with machine learning capabilities like generative AI for easy real-time data interpretation and thus faster, better-informed decision-making. For this reason as well as other emerging capabilities, the incorporation of AI technologies and their unique capabilities has generated immense opportunities for evolving manufacturing facilities across the globe, including here in Australia.
AI applications for manufacturing provide a dynamic array of benefits, including equipping manufacturers with the power to perform predictive maintenance that can potentially extend the usable lifespan of floor machinery. But there are far more use cases where AI tools can help manufacturers conserve equipment, reduce energy or materials consumption and waste production, and generally strengthen the sustainability of their operational processes.
However, as an emerging technology, the long-term or holistic benefits of AI applications in manufacturing aren’t widely known. Similarly, it can be difficult for facility managers to contextualise integrating these AI tools into their own factories.
So how is AI being used in manufacturing? What benefits can smart manufacturing solutions provide? And are there any immediate obstacles or challenges that manufacturers may face when integrating AI solutions onto their factory floors? Our experts at Rayven will be answering these questions today, alongside outlining why AI applications for manufacturing are considered to be a foundational investment for the digital transformation of global manufacturing.
Key Areas for AI Integration in Manufacturing
AI manufacturing solutions can be tailored to specific industries, ensuring that connected AI-enabled technologies, plant machinery, and other digital assets all work together to harvest and analyse data that may aid in systems optimisation.
Here are just some of the key areas where the manufacturing sector can most benefit from investing in AI integration...
Continue reading How is AI Used in Manufacturing?
When you think about robotics in manufacturing, chances are your mind still conjures up images of Hollywood sci-fi movies – but the future is here.
Generative artificial intelligence (AI) technologies are set to play a pivotal role in the digital transformation of manufacturing facilities both across Australia as well as globally. By providing smart solutions for real-time data collection and analysis, AI manufacturing applications powered by tailored LLMs (large language models) are poised to boost both the efficiency and sustainability of manufacturing enterprises.
Similarly, with the advent of climate-conscious industrial practices, maintaining ‘futureproof’ enterprises will naturally require management teams to adopt a triple bottom line approach that aids in meeting sustainability goals and balancing ESG performance. Industrial AI tools also support Australian manufacturers in maintaining this triple bottom line approach – and in more ways than one too.
So how has manufacturing revolutionised in recent years, and what changes are still yet to come? From manufacturing facility management, machine maintenance, plant quality control, transportation and logistics management, and even data interpretation and decision-making, our experts at Rayven will be answering these questions today by outlining how AI manufacturing applications are being integrated in facilities across Australia. We’ll also touch on what the future of automation in manufacturing is likely to look like based on projected trends.
What is AI in Manufacturing?
Artificial intelligence has been integrated into the manufacturing sector by way of providing centralised platforms wherein manufacturers can manage connected industrial IoT technologies. These platforms allow manufacturers to maintain a whole systems approach to factory line management. From controlling materials consumption, and energy or other resource inputs to monitoring output and line profitability, AI manufacturing tools provide a holistic overview of all aspects of your manufacturing operation...
Continue reading The Future of Manufacturing: How AI is Helping Factories Evolve.
Overall Equipment Effectiveness (OEE) measures the six big causes of lost production, providing organisations with an overall measure of asset utilisation.
The term was created by Seiichi Nakajima, the founder of the Total Productive Maintenance system, and is based on the Harrington Emerson way of thinking regarding labour efficiency, to provides you with a single score for your manufacturing performance.
As a measure, it’s useful for manufacturers in lots of ways, primarily however, it provides manufacturers with a way to compare and contrast its performance in numerous ways, (such as line x line, between products, facilities or regions) to see how effective they’re being vs. the maximum potential output of their manufacturing process.
The difficulties of measuring OEE and why IoT fixes that.
Measuring OEE is difficult because there’s lots of moving parts, machines aren’t necessarily networked, comms are limited, technology hasn’t historically been up to scratch.
What this has led to is lag measures of OEE, sometimes still done manually, based on a snapshot of performance after the fact – meaning that by the time you know what your score is, it’s too late to do anything about. Not only that, without transparency into the individual inputs that are going in to make that score over long periods of time, it can be incredibly difficult to spot trends hidden in the data that could be invaluable to the business.
IoT changes this. Not only can you retrofit old machinery and technologies to collect data about their performance – reducing the need for expensive capital-intensive investment – but the flexibility of some manufacturing IoT solutions means that you don’t need to change how you’re currently operating to incorporate it (or until you have the data at hand to do it to make improvements)...
Continue reading The Benefits of Measuring OEE in Real-Time with IoT.
Overall Equipment Effectiveness (OEE) is a critically important measure for manufacturers, but measuring OEE accurately, consistently and at any given moment can be incredibly difficult for manufacturers.
Textbook vs. real-time OEE measurement.
OEE provides managers with an overall measure of asset utilisation and enables them to identify where major issues are, enabling them to focus improvement activities so that you can improve the bottom-line.
Whilst there’s a best practice technique for measuring it, every organisation has a different approach and because every manufacturing plant runs in its own way, there are always variations. For example:
- What’s your access to data? Some tools have accessible PLC or SCADA output with downtime reasons, others have closed PLCs or none, so need external sensors.
- Is a scheduled break a preventable loss? Some say ‘no’, but staff might be able to be rotated through breaks to keep the line running.
- Some data is only accessible through manual extractions or cannot be connected to networks, meaning that you only get data once its use is already reduced.
- How are they coded? Every business has a different set of reason codes, and these may well need to be changed over time.
What’s common to all manufacturers is that you need to know what your baseline OEE calculation is before you can monitor it - even this can be a difficult...
Continue reading Establishing Real-Time OEE: How IoT Can Change Everything (for the Better).
Security is top-of-mind when it comes to just about every technology, but with IoT, it’s even more important.
If a manufacturer is looking to deploy IoT technology into the manufacturing process, this ratchets up security’s importance from high to business-critical because the impact of a cybersecurity breach might be more than an annoyance and a password change, it could be ruinous.
Beyond security, the measures put in place to safeguard your data streams are, in many cases, the same ones required to guarantee a clean and reliable flow of data into your IoT platform, without which your IoT solution cannot properly function.
IoT security at every layer.
Complete IoT solutions have many, many components and (figurative and literal) moving parts. This makes looking at each of them individually a bit more complicated, so the best way to break it down is into three key areas...
Continue reading Manufacturing: How to Run IoT Technology & Measure OEE Securely.
Unless you’ve been hiding under a rock, you’ll have come across talk of industrial IoT, data science and machine learning in the manufacturing sector, but what exactly are they and how should you be using them in your manufacturing organisation?
The worst and best bit: they can do anything.
Truly, they’re a bag of tricks which can be customised, combined, tweaked and applied to just about any process, existing technology set, or utilised to create an all-new, transformative solution.
Before we go further, let’s start with the basics: what is Industrial IoT, Data Science and Machine Learning and how do they apply to manufacturing?
Continue reading How you can use Industrial IoT, Data Science and Machine Learning in Manufacturing (and Why).