Welcome to Industry 4.0 or the Fourth Industrial Revolution! A product of the digital age, Industry 4.0 advancements have paved the way for industrial technologies with machine learning capabilities like generative AI for easy real-time data interpretation and thus faster, better-informed decision-making. For this reason as well as other emerging capabilities, the incorporation of AI technologies and their unique capabilities has generated immense opportunities for evolving manufacturing facilities across the globe, including here in Australia.
AI applications for manufacturing provide a dynamic array of benefits, including equipping manufacturers with the power to perform predictive maintenance that can potentially extend the usable lifespan of floor machinery. But there are far more use cases where AI tools can help manufacturers conserve equipment, reduce energy or materials consumption and waste production, and generally strengthen the sustainability of their operational processes.
However, as an emerging technology, the long-term or holistic benefits of AI applications in manufacturing aren’t widely known. Similarly, it can be difficult for facility managers to contextualise integrating these AI tools into their own factories.
So how is AI being used in manufacturing? What benefits can smart manufacturing solutions provide? And are there any immediate obstacles or challenges that manufacturers may face when integrating AI solutions onto their factory floors? Our experts at Rayven will be answering these questions today, alongside outlining why AI applications for manufacturing are considered to be a foundational investment for the digital transformation of global manufacturing.
Key Areas for AI Integration in Manufacturing
AI manufacturing solutions can be tailored to specific industries, ensuring that connected AI-enabled technologies, plant machinery, and other digital assets all work together to harvest and analyse data that may aid in systems optimisation.
Here are just some of the key areas where the manufacturing sector can most benefit from investing in AI integration.
Improved Decision-Making with Generative AI-Powered Data Analytics
Generative AI applications in manufacturing are capable of monitoring machine energy consumption in relation to other variables like production output. By analysing key variables like machine unit productivity, resource utilisation, and materials waste production resulting from facility operations, AI tools allow manufacturers to improve these operational processes holistically, namely by making data-driven decisions using real-time data analytics capabilities that ultimately reduce machine downtime, optimise resource utilisation, and boost the productivity and profitability of manufacturing lines.
Similarly, with the advancement of generative AI capabilities that use LLMs (large language models), all of your facility’s operational data can be easily interpreted by simply asking your AI tools the right questions. In other words, you don’t need to analyse the data yourself, but simply ask your AI manufacturing solution for the answers you seek, be they related to machine downtime, energy consumption trends, or all the other factors that contribute to your facility’s overall operational performance.
If you want to start asking your GenAI-powered data analytics tools questions like ‘how can I boost production yields?’, however, then you need to ensure that your AI tool has plenty of operational data to draw from. This in a nutshell, is why early adoption of generative AI data tools is so vital for maintaining a competitive advantage for your business in the digital age. Getting in on the ground floor of this tech helps ensure that your enterprise generates data insights before your competitors both immediately and over the long term, as your AI tool reaches heightened levels of sophistication the more it’s exposed to your company’s unique performance data.
Facilitating Quality Control with Anomaly Detection & Predictive Maintenance
Machine learning technologies use pattern recognition to accurately detect production defects as they occur. This supports quality control processes in manufacturing industries, reducing the likelihood of defects being found amongst finished, market-ready products.
Sensor technology can also be used to detect anomalies in the quality or appearance of final products. Defects or anomalies that are found can then be recognised in future by AI applications, automating quality inspection processes with formulaic accuracy.
But the quality control capabilities of AI applications in manufacturing don’t just stop at product quality. By using predictive analytics, AI applications can also identify breakdowns or inefficiencies in machine operations, and perform tailored predictive maintenance that extend the usable life of factory machines. With an assurance of optimally operational machinery, manufacturers can focus on product development rather than allocate resources for repair or replacement of equipment or machines.
Improved Supply Chain Management with Supply Chain Tracking
The universal compatibility of AI solutions support manufacturers when it comes to materials supply chain management and even product distribution. From route management and monitoring performance of IoT-enabled fleets, to using sensor technology for periodic assessments of storage conditions, AI applications in manufacturing can also provide a whole systems approach to supply chain tracking.
Opportunities for Product Innovation with No-Code Toolkits
For manufacturers who produce specialised goods like hardware and IoT devices or even automotive or auto parts manufacturing, AI applications can actually aid in optimising product design, development, and customisation to suit unique markets. Generally, this can be done by gathering data relating to customer retention and satisfaction and then using these insights to make improvements to existing products or even develop new products.
But Rayven takes product innovation capabilities one step further with the provision of easy-to-use toolkits and codeless interfaces, made available through our AI solutions. Using these kits and interfaces, our users can actually develop their own Industry 4.0 functionality and AI, ultimately creating finished products that are optimised for commercial success.
Workforce Quality Enhancement with Integrated Smart Technologies
AI applications can connect up to virtually all technologies – including IoT-enabled fleets and wearable worker technologies. This means that senior management teams can now monitor not only the productivity of manufacturing lines, but also factory floor and staff safety.
By conducting AI-driven risk assessments and mitigation processes as well as detecting worker incidents or even potential incidents (i.e. from staff moving into high-risk zones), AI applications in manufacturing can aid in boosting the quality of manufacturing floors and other similarly heavy-duty industrial environments.
Case Studies of AI Integration in Manufacturing
AI integration can provide myriad benefits to a range of manufacturing industries, including automotive or aerospace unit and parts production, consumer and industrial electronics or hardware production, food and beverage manufacturing, and even pharmaceuticals development and packaging.
Some of the most compelling case studies for AI integration in manufacturing actually include food manufacturing (due to the requirement for high accuracy storage condition monitoring), dynamic manufacturing line optimisation, and fleet monitoring.
Using AI in Food Manufacturing
When developing an AI solution for food manufacturing, there are a number of operational performance metrics that platforms need to be built around. These include:
- weight sensors for weighing units,
- smart thermometers and air quality monitoring systems for monitoring environmental metrics,
- ERP (enterprise resource planning) systems for collecting daily production targets, and comparing unit weights to target weights or package sizes for uniformity,
- IoT-enabled machinery for predictive maintenance and reducing machine downtime, and,
- Real-time OEE solutions for holistic data management.
OEE (overall equipment effectiveness) solutions aid in monitoring all operational performance metrics across manufacturing lines. In the context of food manufacturing, OEE systems are tasked with recording all the variables that are gathered by the above AI-driven technologies. Maintaining access to these metrics from a centralised viewpoint allows manufacturers to maintain productivity and quality control both across their manufacturing line and even during product storage or refrigeration.
Using AI for Manufacturing Line Optimisation
Another reason why food manufacturing case studies demonstrate the most compelling benefits of AI tools is simply in designing and maintaining systems for managing perishable products with a minimal shelf life. As these perishable products require prompt production processes to reduce product waste, optimal manufacturing lines are a vital investment for ensuring plant profitability and sustainability. Thankfully, AI-driven manufacturing line solutions can develop optimised production processes using target goal inputs, ensuring reduced downtime between units and minimising delays between production and distribution.
These benefits also apply for manufacturing facilities that aren’t actually producing products for consumer markets, but are rather recycling used materials and are thus, looking to keep their resource consumption and waste production low. For instance, Rayven’s experience with developing plastic recycling plant AI solutions involved prioritising reduced stoppages and energy consumption, ensuring that the recycling plants maintained optimal, sustainable manufacturing line operations.
Using AI for Fleet Monitoring
The production line doesn’t just stop at the factory floor. Today, manufacturers are also tasked with considering distribution systems for maintaining the quality of their products before it hits the market and is directly available to consumers.
This is where fleet monitoring solutions can aid in ensuring a whole systems approach to manufacturing line optimisation. By being able to monitor temperatures in refrigerated trucks, optimise fleet routes, and monitor fleet maintenance, AI fleet monitoring solutions can reduce risks of transportation delays or other logistical concerns that may result in product waste.
Challenges & Solutions To AI Integration for Manufacturing
Despite the undeniable benefits of AI applications for the manufacturing sector, there are some barriers that have prevented Australian manufacturers from adopting these technologies. As our mission at Rayven is to remove those barriers, we’ll be sharing some of the top challenges to AI integration in the manufacturing sector, and how our AI solutions have been designed to mitigate these challenges and maintain accessibility for Australian manufacturers.
The Challenge: Enterprises don’t have money to invest in AI solutions and OEE monitoring
Centralised AI manufacturing solutions are made up of many different components, some of which may involve some higher upfront costs (i.e. swapping out outdated machinery for machines with predictive maintenance and other AI-enabled features). For established manufacturing facilities, making these digital transformation investments will naturally require an extensive growth strategy and accompanying strategy budget.
The Solution: Invest in scalable solutions that grow with your business
The benefit of Rayven’s AI-driven manufacturing solutions are that they’re expressly designed to provide scalability. The universal compatibility of our AI platforms ensures that you can upgrade connected technologies at your own pace, facilitating extensive digital transformation schedules that support the sustainable evolution of your manufacturing facilities.
The Challenge: Enterprises can’t invest in staff training for AI solutions
In all digital transformation strategising, enterprises aren’t just budgeting for hardware or software investments, but also in accounting for staff training to ensure workers are equipped with the ability to use new technologies. Budgeting for staff downtime during training modules and in the development of learning materials naturally requires an additional time investment that may impact manufacturing operations.
The Solution: Invest in easy-to-use AI manufacturing platforms
Rayven’s low-code AI manufacturing solutions are designed to provide intuitive user interfaces and controls. With easy-to-use features like drag-and-drop mechanics for tailoring platforms and connected tools, to versatile data analytics features that support easy data presentation and organisation, our AI manufacturing platforms come with a minimal learning curve and can be used ‘right out of the box’.
The Challenge: Enterprises are uncertain about which solutions they can most benefit from
Throughout this article, we’ve touched upon AI technologies that feasibly could be of value to a dynamic range of manufacturing facilities, depending on their product output. However, it can be difficult for management teams to independently identify which technological offerings are the right for their enterprise, or which ones should be priority investments.
The Solution: Take advantage of Rayven’s pre-built modules
Rayven’s industry-specific applications have actually been designed with Australia’s diverse industries in mind. In fact, our AI experts take pride in developing industrial solutions that are easy to configure to suit the unique needs of your enterprise.
Our Fast Start Brochure has also been designed to support manufacturers in better defining the scope of your transformation strategy, identifying the Industry 4.0 technologies that will be most valuable for your business, and even develop a strategy for solution implementation.
Utilising The Transformative Potential of AI for Manufacturing Industries
Industry 4.0 is still largely uncharted territory for many Australian industries. As more manufacturers engage with how best to integrate and run their technologies sustainably over the long term whilst still ensuring their operational processes stay agile, there is a unique opportunity for enterprises to jump in on the ground floor of these emerging technologies.
Engaging with AI applications in manufacturing now and tailoring solutions to suit your business can provide your facilities with the opportunity to undergo a revolutionary digital transformation before your competitors. Embracing the transformative potential of these technologies now may aid in establishing your enterprise as a fixture of modern manufacturing in Australia, spearheading efficient and sustainable production processes that
Author
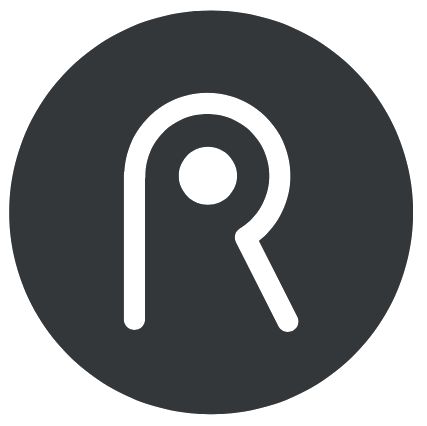